31. HOTSPOT
Case Study
This is a case study. Case studies are not timed separately. You can use as much exam time as you would like to complete each case. However, there may be additional case studies and sections on this exam. You must manage your time to ensure that you are able to complete all questions included on this exam in the time provided.
To answer the questions included in a case study, you will need to reference information that is provided in the case study. Case studies might contain exhibits and other resources that provide more information about the scenario that is described in the case study. Each question is independent of the other questions in this case study.
At the end of this case study, a review screen will appear. This screen allows you to review your answers and to make changes before you move to the next section of the exam. After you begin a new section, you cannot return to this section.
To start the case study
To display the first question in this case study, click the Next button. Use the buttons in the left pane to explore the content of the case study before you answer the questions. Clicking these buttons displays information such as business requirements, existing environment, and problem statements. If the case study has an All Information tab, note that the information displayed is identical to the information displayed on the subsequent tabs. When you are ready to answer a question, click the Question button to return to the question.
Background
Adventure Works Cycles is a high-end bicycle manufacturer in North America. Their standard model bicycles are available year-round. Limited-edition bicycle models are released several times a year to boutique retailers domestically.
Adventure Works has had the most success with their limited-edition bicycles. These bicycles have high margins, are in high demand, and have a strong following with the younger generation biking community.
Current environment
General
Adventure Works expects to triple their manufacturing capabilities in the next few years due to increasing demand. The company plans to invest in Dynamics 365 Finance, Dynamics 365 Supply Chain Management, and the Power Platform products to migrate from a custom-built enterprise resource planning (ERP) solution and Microsoft Excel worksheets.
Adventure Works sells only to the United States and Canada. Despite their limited market, they cannot keep up with current demand. Over time, they want to expand their market to remain pro table.
Adventure Works has no capabilities or budget to undertake any development beyond Excel formula-level tasks.
Bicycle manufacturing
• Bicycle models are measured and reported against how well a single model performs as a sum of all the variations of that model. For example, the Street Kid YOLO model sold 25,000 units in 2019 across all variations of the product, but the Purple Female frame made up 30 percent of that model's sales.
• The Street Kid YOLO models sell in different volumes depending on the market.
• The creation of production orders for bicycles occurs monthly and is based on historical sales.
• Each part of a bicycle’s assembly occurs at a different station in the Adventure Works production facility.
• A piece of paper that has eight sections accompanies a bicycle throughout the manufacturing process. As each step is completed, the respective section is completed and signed off by a production worker.
• The completed paper is used in the put-away process by the warehouse workers.
Financials
• The standard model and limited-edition bicycle teams are separate operating units within the manufacturing division. Financials are tracked and reported separately even though they are produced and sold in the same sales channels.
• Updates to the standard model bicycle models are created when a part for a bicycle becomes unavailable. This can change the cost of the product.
• An updated model of a bicycle with new parts will be maintained as a new item and have a new price. However, it will look like the exact same product to retailers and distributors.
Manufacturing process
The bicycle manufacturing process is shown in the following graphic:
Limited-edition bicycle process
The limited-edition bicycles are made up of an Adventure Works custom frame with all other parts created by local artists and manufacturers.
• Each bicycle has a unique set of new items that make up the bill of materials (BOM) because all parts are created to specification.
• A single pilot limited-edition bicycle is created as a proof of concept.
• Adventure Works occasionally reuses components from existing bicycles, but most limited-edition bicycles are made of handcrafted components designed to specifications.
• Each limited-edition bicycle is built, and hand signed by a single Adventure Works artisan.
• Sales price must be auto calculated after the cost price is derived.
• Before creating the proof of concept limited-edition bicycle, the approximate sales price needs to be determined through a cost-plus 20 percent calculation.
• All items except for the frame in the prototype process are considered finished items and can be sold individually.
• The frame items require modifications in accordance with the manufacturing process as well as painting.
• Each Adventure Works limited-edition bicycle artisan is scheduled to create a specific number of bicycles in a production run that must be completed by a certain date.
• Limited-edition bicycle artisans work exclusively on a given run of limited-edition bicycles and are not able to work on other tasks.
Limited-edition bicycle BOM assembly process
The prototype process for the limited-edition bicycles is shown in the following graphic:
Requirements
General
• Adventure Works will consist of three legal entities: the primary legal entity of the United States (AWUS), sales in Canada (AWCA), and an international expansion (AWIN).
• AWIN must be able to sell only standard model bicycles.
• AWUS and AWCA must be able to sell both standard model and limited-edition bicycles.
• Warehouse workers must use the Warehouse Management mobile application to manage all inventory inbound and outbound from the warehouse.
Bicycle manufacturing
• The handlebars, back wheels, and front wheels must not change for any of the bicycle model configurations.
• Standard model bicycle production scheduling must be configured to start as soon as possible.
• Bicycle components must be automatically reserved when the item is released to the production floor.
• Standard model bicycle production must be automatically created on a predefined schedule.
• As soon as bicycles are completed, they must be available to fulfill the backlog of orders.
• Limited-edition bicycle production must be configured to meet the end date for when the bicycles must be completed.
• Production orders need to track financials by standard model or limited-edition bicycle manufacturing teams.
• The system must log the immediate consumption of BOMs for traceability.
• All inventory is warehouse enabled.
• Finished goods are reported as finished by the warehouse worker who picks up the finished product from the packaging area.
• Finished products must automatically have put-away work completed for them.
New limited-edition bicycle process
Adventure Works is creating a new, limited-edition bicycle to commemorate the company's tenth anniversary. The limited-edition bicycle will be designed for charity events and be produced for the summer season.
• The bicycle must be available in men’s, women’s, and unisex frame styles. It will be painted in one of 50 hand-painted designs representing the charity of the customer's choosing.
• A limited run of 100 bicycles must be created.
• The limited-edition bicycles must use the same production process as the standard model bicycles.
• The limited-edition bicycles must use the same parts used for previous limited-edition bicycles, except for the unique paint colors.
• Frames must be painted in-house.
• Five painting options are available only in the unisex frame style.
New limited-edition bicycle orders
• Customers must be able to place sales orders for the item in the chosen frame configuration, including style and color.
• When an order for the new limited-edition bicycle is created, payment must be provided.
• An approval for an order must exist for the order to be processed
• Upon approval of an order, production must start immediately and not require re-entry of data.
You need to configure the options for the new limited-edition bicycle for the summer season.
Which configurations should you use? To answer, select the appropriate options in the answer area
NOTE: Each correct selection is worth one point.
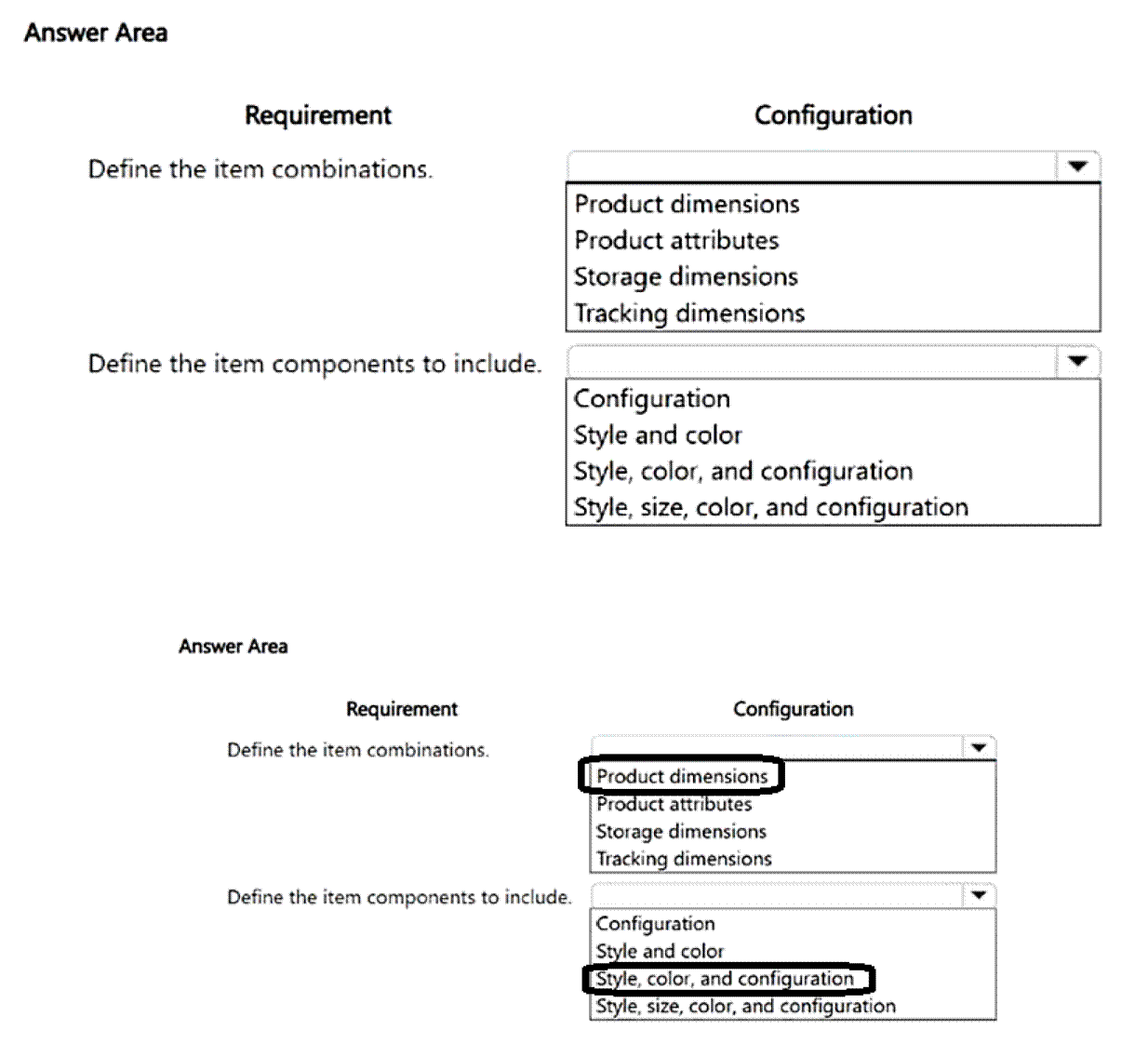